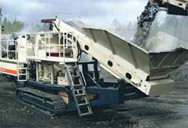
equipment to increase iron ore quality
SKD equipment to improve iron ore quality in Ukraine. Sep 07, 2012· SKD equipment to improve iron ore quality in Ukraine. 7 September 2012 Roisin Reidy The SKD delivery includes high-capacity vertical grinding mills, flotation cells, magnetic separators, 59 pumps and a crushing and screening system.
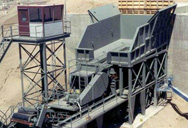
Iron ore - Wikipedia
09-11-2002 · Lower-grade sources of iron ore generally require beneficiation, using techniques like crushing, milling, gravity or heavy media separation, screening, and silica froth flotation to improve the concentration of the ore and remove impurities. The results, high-quality fine ore powders, are known as fines. Magnetite. Magnetite is magnetic, and hence easily separated from the gangue minerals and ...
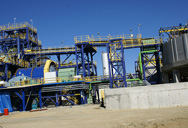
Influence of Coating Granulation Process on Iron …
To improve the sinter quality and productivity for low grade iron ore fines, different granulation processes like the conventional one, and other two advanced granulation processes like coke breeze, and flux & coke breeze coating granulation were studied in detail by conducting laboratory pot grate sintering experiments.
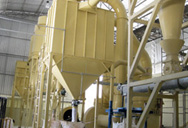
Quality Management of Iron ore and coal by Raw Material ...
Quality Management of Iron ore and coal by ... Reduce Alumina in Iron ore fines Improve Beneficiation Capability ... directly or indirectly- improve KPI status 3. Develop processes to serve long term and short term needs of customer :Management System Chart for QA 4.
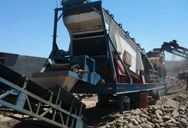
Influence of Coating Granulation Process on Iron …
To improve the sinter quality and productivity for low grade iron ore fines, different granulation processes like the conventional one, and other two advanced granulation processes like coke ...
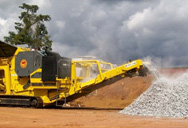
Iron processing | Britannica
14-08-2020 · Iron processing, use of a smelting process to turn the ore into a form from which products can be fashioned.Included in this article also is a discussion of the mining of iron and of its preparation for smelting. Iron (Fe) is a relatively dense metal with a silvery white appearance and distinctive magnetic properties. It constitutes 5 percent by weight of the Earth’s crust, and it is the ...
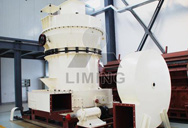
iron ore quality Archives - Process productivity
iron ore quality The relevance and application of textural information across the value chain Changes in the iron ore industry have been a huge point of discussion over the last year.
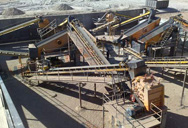
Iron ore production scheduling to improve product …
Iron ore quality depends upon successive shipments being uniform in composition, not only in iron but also in several other minerals. The production process involves several stages of scheduling, from the mine face, through railing, stockpiling and ship loading.
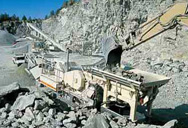
Understanding iron ore analytical tools. - Process ...
By Keith Vining. The 7 analytical tools you can use to improve mine performance. The utilisation of increasingly goethitic ore deposits in Australia has created a greater need for the iron ore supply chain to adopt the use of new tools and analysis techniques in order to understand goethite properties, and continue to drive operational efficiencies. ...

Iron Ore Mineral Dressing Processes Customer Case
Iron Ore Production Scheduling To Improve Product Quality. Mar 01 2001nbsp018332iron ore quality depends upon successive shipments being uniform in composition not only in iron but also in several other minerals the production process involves several stages of scheduling from the mine face through railing stockpiling and ship loading. Read More >

Sinter Quality and Process of Sintering Iron Ores – …
Fig 1 Schematics of sinter mix and product sinter Sintering process is a generic term that is used to describe the process of agglomeration of a green mix of iron ores, fluxes and coke and plant solid wastes having a particle size of -10 mm so as to produce sinter which can withstand operating pressure and temperature conditions existing in a BF.
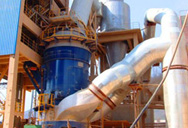
3D Stockpile Modelling to Improve the Quality Control in ...
Abstract-This stone describes a 3D stockpile modelling algorithm to improve quality control and increase operational efficiency in iron ore handling. The 3D model, generated from real measuring data, approximates a stockpile using a group of 3D volumetric element, which able to store information inside it, such as quality compositions of the ore.
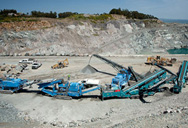
Metal Types and Recycling Process
25-06-2019 · Steel and iron are the most recycled materials in the world due in part to the opportunity to recover large structures as well as the ease of reprocessing. The use of magnets in the sorting process enables recyclers to easily separate them from the mixed waste stream. Every year, around 400 million tons of metal are recycled worldwide.
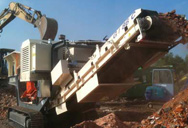
Iron Ore Reduction - an overview | ScienceDirect …
The proposed process was modeled in two configurations: 1-step and 2-step processes in which the number of iron ore reduction reactor is different. Simulation was performed under various operating conditions to examine the effect of operating conditions on the fresh hydrogen amount which would affect the economic feasibility greatly due to expensive hydrogen price.
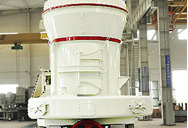
Iron Ore Pelletizing Process: An Overview | …
10-07-2017 · The iron ore production has significantly expanded in recent years, owing to increasing steel demands in developing countries. However, the content of iron in ore deposits has deteriorated and low-grade iron ore has been processed. The fines resulting from the concentration process must be agglomerated for use in iron and steelmaking.
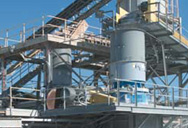
IRON ORE SINTERING PART 2. QUALITY INDICES …
Improvements in the blast furnace process are achieved by technological improvements and a stable supply of high quality iron ores and sinters [1]. However, high quality iron ore resources are being depleted due to the heavy demand, and thus it is necessary to continue improving sintering technology in order to use lower quality iron ores in the raw mix.
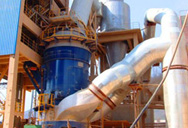
Wrought iron - Wikipedia
Wrought iron is an iron alloy with a very low carbon content (less than 0.08%) in contrast to that of cast iron (2.1% to 4%). It is a semi-fused mass of iron with fibrous slag inclusions (up to 2% by weight), which gives it a "grain" resembling stone that is visible when it is etched or bent to the point of failure. Wrought iron is tough, malleable, ductile, corrosion-resistant and easily welded.
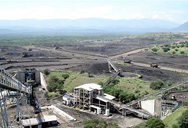
Iron Ore Processing for the Blast Furnace
blast furnace process. The iron ore concentrate is now mixed and ready for the pelletizing process. Pelletizing A pellet plant contains a series of balling drums where the iron ore concentrate is formed into soft pellets, in much the same manner that one rolls a snowball, to make a pellet about the size of a marble (between 1/4" and 1/2").
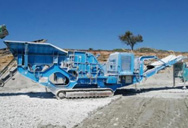
Iron processing - Ores | Britannica
Iron processing - Iron processing - Ores: Iron ores occur in igneous, metamorphic (transformed), or sedimentary rocks in a variety of geologic environments. Most are sedimentary, but many have been changed by weathering, and so their precise origin is difficult to determine. The most widely distributed iron-bearing minerals are oxides, and iron ores consist mainly of hematite (Fe2O3), which is ...