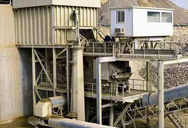
Cement Industry | Loesche
Social media. Instragram; Facebook; Twitter; Linkedin; Xing; Youtube; Slideshare; Cement Industry . LOESCHE Vertical Roller Mill: We do much more than rely solely on our unbeatable technology. Our designers are constantly coming up with new ideas and even more dependable components to reduce the already acclaimed low failure rate of our mills. The roller grinding mill technology, patented in ...
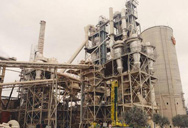
Progress with Grinding Aids for Vertical Roller Mills
The effect of grinding aids on the comminution of cement is based on the dispersion of fine particles. It is a misunderstanding that grinding aids for vertical roller mills (VRMs) should stabilise the material bed between the rollers and the table by adhesive forces between the particles. Grinding aids reduce the polarity of the cleaved surface and the attraction forces between particles.
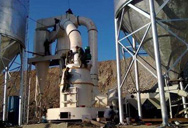
Grinding Roller Manufacturer From China - …
Grinding roller of vertical mill. Weight :20-120 t. Material: ASTM: 1030 / DIN: 30Mn4. Application:Vertical mill,Slag vertical mill, Cement vertical mill etc. Customizable: Yes. MOQ:1 Piece/Pieces castings. Place of origin: Henan, China(Mainland) Contact us for more information on how this product can help you with your unique requirements.
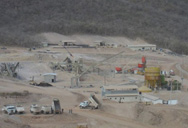
Ball Mills Or Vertical Roller Mills: Which Is Better …
Regarding operations, in a ball mill, the grinding media has a higher rate of wear about the rollers and table in the VRM. In ball mills, it is essential to monitor its performance via axial testing to ascertain that the media grading is right and that there are enough top-size media to grind the mill feed materials. If not so, high, underground materials (referred to as nibs) will collect around the edge of the first chamber.
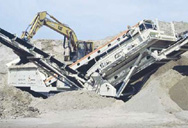
Cement grinding Vertical roller mills versus ball mills
Cement grinding Vertical roller mills versus ball mills Soeren Worre Joergensen MSc, General Manager, Engineering, Grinding Technology F.L.SMIDTH . 2 Introduction Around 110 years ago a Danish engineer, M. Davidsen, patented a pioneering invention in France which involved a tube mill with a charge of steel balls or flint pebbles for fine grinding of sand or cement. F.L.Smidth acquired the ...
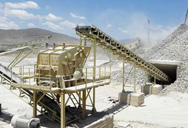
PROCESS DIAGNOSTIC STUDIES FOR CEMENT MILL …
quality spare parts and consumables like grinding media . Ball mills are predominantly used machines for grinding in the cement industry. Although ball mills have been used for more than one hundred years, the design is still being improved in order to reduce the grinding costs. HOLTEC has undertaken Performance Optimisation of the cement grinding circuits by doing process diagnostic studies ...
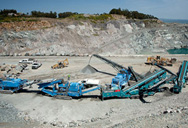
Coal Mills for Cement Plants | Loesche
Coal grinding mills ... LOESCHE has been able to convince the cement division of the Chaudhary Group (CG Group) of the advantages of its vertical roller mill technology. LOESCHE has managed to gain a new customer in Nepal, namely the cement division of the Chaudhary Group based in Kathmandu. VIEW MORE. Coal The coordinates of the grinding table diameter and number of rollers can be read …
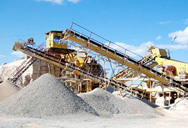
Roller Mills | Milling | Bühler Group
The grinding gap on our roller mills can be adjusted manually or, on some models, automatically. If you adjust the grinding gap automatically, the adjustment can be based on your recipe or on particle size. This enables you to produce a consistent and high quality of stone and semolina. Safety. Designed for a high level of operational safety. Our roller mills are designed for the highest ...
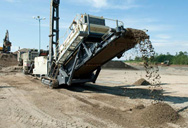
Finding failure - International Cement Review
06.09.2017 · During mill operation roller surfaces wear down, which results in a higher dynamic load, peaks which exceed the nominal torque and, in general, an instable mill operation and lower performance. In many instances, bearing failures at the rolls are caused by excessive dynamics in the grinding process. The Dalog Torque Sensor D-TS 100 (Figure 6) is a direct measurement system …
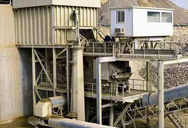
Cement mill - Wikipedia
These have been used for many years for the less exacting raw-milling process, but recently roller mills, in combination with high-efficiency separators, have been used for cement grinding. The grinding action employs much greater stress on the material than in a ball mill, and is therefore more efficient. Energy consumption is typically half that of a ball mill. However, the narrowness of the particle size …
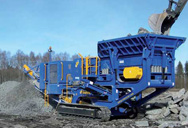
OK™ cement mill The most energy- efficient mill for cement ...
Proven commercially, the OK™ mill is the premier roller mill for finish grinding of Portland cement, slag and blended cements. The mill consistently uses five to ten percent less power than other cement vertical roller mills, and in comparison with traditional ball mill operations, the energy requirements for …
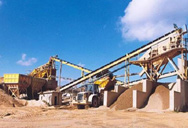
Gebr. Pfeiffer to supply the world’s largest vertical ...
01.11.2011 · Holcim (Brasil) S.A. has awarded the Spanish EPC leader Cemengal a contract to supply a state-of-the-art cement grinding station to increase the capacity of its Barroso works located in the Brazilian state of Minas Gerais. Acting as main contractor for this grinding project, Cemengal ordered an MVR 6700 C-6 roller mill from Gebr. Pfeiffer SE which with its production capacity of up …
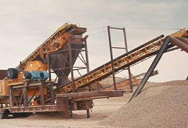
OK™ mill The most reliable and efficient mill for raw and ...
nance inside the mill. When the roller grinding surfaces are worn, the tire segments can either be replaced or they can be re-welded, without removing the rollers from the mill. The swing-out feature allows rollers to easily be removed from the mill, allowing the possibility to perform maintenance work externally from the mill. Common OK™ mill roller assembly for raw and cement mill. OK ...
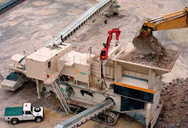
Energy-Efficient Technologies in Cement Grinding …
23.10.2015 · Vertical roller mills are developed to work as air-swept grinding mills. Roller mills are operated with throughput capacities of more than 300 t/h of cement raw mix (Loesche mill, Polysius® double roller mill, Pfeiffer® MPS mill). Loesche roller mill and Polysius® roller mills are widely applied in cement raw material grinding. Schematical view of a Pfeiffer MPS mill is given in Figure 5 ...
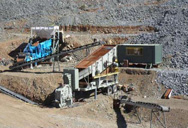
Overview of our mills · Christian Pfeiffer
The roller press is often used where energy-efficient grinding of large product quantities is required. The two rollers, rotating in opposite directions, exert very high pressure on the material, effectively crushing and weakening the particles (microscopic cracks), so that the subsequent fine grinding is easier. When used as a pre-grinding system in ball mill circuits, production increases of ...
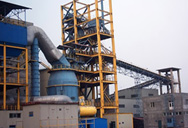
MVR vertical roller mill for cement grinding
Wonder Cement switches to Pfeiffer vertical roller mill for cement grinding. Wonder Cement belongs to a family company based in Udaipur, India, which – apart from other businesses – is active in the cement industry. As Gebr. Pfeiffer already supplied 4 mills of the type MPS for raw material and stone coke grinding, the customer has now decided to use a vertical roller mill also for cement ...

Loesche supplies four vertical roller mills (VRM) …
08.07.2018 · One high-performance 4-roller mill VRM with a capacity of 450 t/h is to be used there for the grinding of cement raw material to a fineness of 12 % with sieving residue of R 90 μm. Two further Loesche mills from the middle performance range and a throughput of 170 t/h will serve for the subsequent grinding of cement clinker to a fineness of 3200 Blaine. One more large …